b.
Cleaning. Refer to paragraph 6-3.a for general
clean-ing instructions.
(1)
Clean fuel filter (2) using ultrasonic cleaner
(Table 2-1).
c.
Inspection. Refer to paragraph 6-3.b for general
in-spection instructions.
(1)
Replace diaphragm (1) if deformed or
cracked. (2) Replace filter (2) if rim or
screen is cracked or broken.
d.
Repair or Replacement. Refer to paragraph 6-
3.c
for
general
repair
or
replacement
instructions.
(1)
Replace a deformed or cracked diaphragm
(1).
(2)
Replace fuel filter (2) if rim or screen is
cracked or broken.
e.
Assembly. To assemble the fuel feed pump
assem-bly, proceed as follows:
(1)
Position fuel filter (2) on pump base. Place
gasket (3) in top cover, and position top
cover on base over fuel filter (2). Attach
cover to base using gasket and screw (4).
(2)
Insert diaphragm (1) into lower body and
join both halves of the pump body using
washer and screws (5).
6-38. Fuel Injection Pump Assembly (Figure 8-35). If
fuel injection pump requires rework or repair, replace
injection pump and send pump to be repaired to a Bosch
Repair Center or equivalent. Time engine with new
pump in accordance with DIESEL ENGINE ASSEMBLY,
(Sec. VI, paragraph 6-33, e).
6-39. Fuel Injector Assembly (See Figure 8-36). The
following paragraphs contain disassembly, cleaning,
inspection,
repair
or
replacement
and
assembly
instructions for the fuel injector assembly.
a.
Disassembly. Only when test results are not
within limits should the fuel injector assembly be
disassembled.
Disassemble
the
injector
assembly only to the extent neces-sary to repair
or replace a defective part or parts.
CAUTION
Under no circumstances should the nozzle, valves. and
discs
be
interchanged.
To
avoid
interchanging, disassemble and reassemble one injector
at a time.
CAUTION
Disassemble the fuel injector in a clean, well-lighted work
area isolated from the rest of the shop.
(1)
Separate retainer nut (1) from nozzle holder
(7).
(2)
Remove shim/s (2), pressure spring (3),
and pressure spindle (4) from intermediate
disc (5).
(3)
Separate disc (5) and nozzle (6).
b.
Cleaning. Refer to paragraph 6-3.a for general
clean-ing instructions.
NOTE
Do not allow parts to remain in dry cleaning solvent for
extended periods of time or rust spots may form. If parts
are not to be inspected immediately after cleaning, dip
them in engine oil per Military Specification MIL-- 2104 or
equivalent.
(1)
All components shall be cleaned and
washed out thoroughly in solvent. Federal
Specification P-D-680, Type II.
(2)
Dry parts with low pressure compressed air
(30 psig maximum).
NOTE
Do not be too hasty in judging the perform-ance of a
nozzle. It has been found that after soaking nozzles in
solvent for a day, that many will meet specifications for
leakage or opening pressure that might otherwise be
rejected.
(3)
After the nozzle (6) has soaked in solvent,
use a brass wire brush to remove any
remaining carbon or fuel stains from the tip.
See Figure 6-21.
(4)
Clean the orifice holes in the nozzle valve
body tip. Use a cleaning wire protruding
only 1/16 inch (1.5875 mm) out of the pin
vise
for
best
6-59
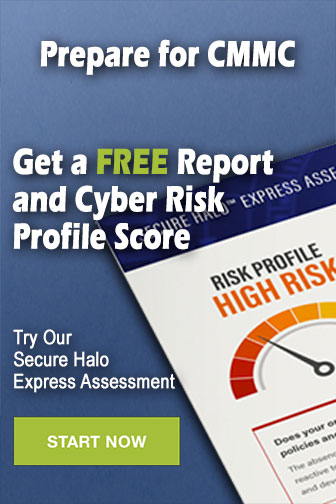