SECTION IV.
OPERATION INSTRUCTION
4-1.
GENERAL. This section describes the theory of
operation, operating procedure, and the operating
controls and indicators for the air compressor unit. The
air compressor unit is designed to deliver contaminant
free, dry breathable air under pressure up to a maximum
of 3,200 psig (22,048 kPa) at a rate of 20 cfm. Air supply
cylinders, 3500 psig (24115 kPa) may be serviced by the
air compressor unit.
4-2.
THEORY OF OPERATION. The reciprocating
air compressor assembly is connected to the diesel
engine power source by means of a manually operated
clutch. Normal operating speed of the diesel engine is
2150 RPM. In the air compressor assembly, air is
compressed to the desired pressure in four separate
stages. The engine speed is controlled manually and
protected by the internal engine governor control.
4-3.
AIR COMPRESSING MODE (Figure 4-1). As
the first compression stage piston travels downward, the
pressure differential causes the first compression stage
intake valve to open, drawing air from the atmosphere
through a dry element type air cleaner into the first
compression stage cylinder. As the first stage piston
travels upward the intake valve closes allowing the air
trapped in the cylinder to be compressed to a pressure of
55 ± 5 psig (379 ± 34.5 kPa). This air then passes
through the first stage air cooler subassembly and the
first stage trap which reduces the air temperature due to
compression heat and removes oil and condensate prior
to the air entering the second compression stage
cylinder. As the second compression stage piston starts
to travel downward, the pressure differential causes the
second stage intake valve to open, admitting the air from
the first stage air cooler subassembly into the second
compressor stage cylinder. When the second stage
piston starts to travel upward; the second stage intake
valve closes, allowing the air trapped in the cylinder to be
compressed to a pressure of 195 ± 10 psig (1344 ± 68.9
kPa). This air then passes through the second stage air
cooler subassembly and second stage trap for cooling
and removal of oil and condensate prior to the air
entering the third stage compression cylinder. As the
third compression stage piston starts to travel downward,
the pressure differential causes the third stage intake
valve to open admitting the air from the second stage air
cooler subassembly. When the third stage piston starts
to travel upward, the third stage intake valve closes,
allowing the air trapped in the cylinder to be compressed
to a pressure of 900 ± 50 psig (6201 ± 344.5 kPa). This
air then passes through the third stage air cooler
subassembly
and third stage trap for cooling and removal of oil and
condensate prior to entering the fourth compression
stage cylinder. As the fourth stage piston starts to travel
downward, the pressure differential causes the fourth
stage intake valve to open admitting the air from the third
stage air cooler subassembly. When the fourth stage
piston starts to travel upward, the fourth stage intake
valve closes allowing the air trapped in the cylinder to be
compressed to a pressure of 3,200 ± 25 psig (22,048 ±
172.3 kPa). This air then passes through the fourth
stage air cooler subassembly which reduces the
temperature of the air. The air then passes through the
mechanical filter where airborne foreign particles and
moisture are removed. The partially clean air
is then directed through the rupture disc (4,400 psi) to
the first (No. 1) dehydrator then to the second (No. 2)
dehydrator, where the air is thoroughly dried of
condensate and oil.
4-4.
Attached to dehydrator (Cyl. No. 2) is the
priority valve which maintains correct pressure for proper
circulation within the air purification cylinders. The
priority valve is set to open at 2,300 psig (15,897 kPa).
From the priority valve the air passes through the air
purification cylinders before it flows through the ten
micron filter where airborne particles larger than ten
microns are removed.
4-5.
A method of continuous removal of moisture
collected in the first, second, and third stage traps is
provided. Removing this moisture, as it is separated,
allows the compressor to operate for an extended period
of time without unloading. The air allowed to bleed-off
will not appreciably reduce the pressure of the output
service air, but it will result in a slight increase in the
pressure of the first stage air. The first stage trap
continuous bleed valve generates a one psi pressure
differential across the valve orifice. This differential
allows the bleed valve to crack, allowing a small amount
of the moisture laden pressurized air to bleed off through
the first stage trap filter and line strainer to the
condensate receiver. As pressurized air from the second
stage compression cylinder passes through the second
stage trap it generates a pressure differential in the
second stage trap continuous bleed valve, 195 ± 10 psig
(1344 ± 68.9 kPa) downstream of the valve and 14.7 psi
(101.3 kPa) upstream of the valve. The second stage
continuous bleed valve will open, causing the first stage
trap continuous bleed valve to open. This will allow a
small amount of moisture laden, pressurized air to bleed
off through the second stage trap filter, second stage line
4-1
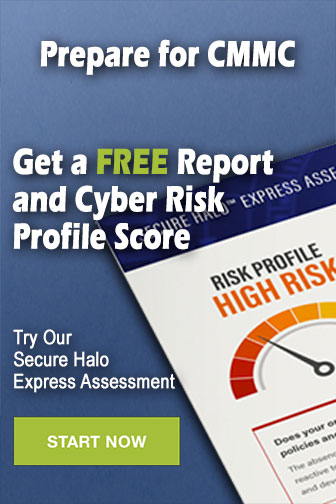