4-24.
SERVICE HOSE BLEED VALVE (13, Figure 4-
3). The SERVICE HOSE BLEED VALVE relieves all air
pressure from the Service Hose. Opening the valve, by
turning counterclockwise, will vent the air in the service
hose to atmosphere.
4-25.
MECHANICAL FILTER DRAIN VALVE (14,
Figure 4-3). The MECHANICAL FILTER DRAIN VALVE
relieves all air pressure from the air compressor through
the mechanical filter. Opening the valve, by turning
counterclockwise, will vent the air to atmosphere.
4-26.
DEHYDRATOR BLEED VALVE (15, Figure 4-3).
The DEHYDRATOR BLEED VALVE relieves all air
pressure from the mechanical filter through to the service
outlet. Opening the valve, by turning counterclockwise,
will vent the air in this line to atmosphere.
4-27.
COMPRESSOR
UNLOADER
SWITCH
(16,
Figure 4-3). The COMPRESSOR UNLOADER toggle
switch serves two functions. When placed in the
UNLOAD position the compressor oil pressure switch is
bypassed, enabling the engine to be started. Since no
current passes through the normally open solenoid valve,
the compressor can be started unloaded. When
compressor oil pressure develops after engaging the
clutch, the UNLOADER SWITCH is placed in the LOAD
position and the compressor begins to load.
4-28.
PUSHBUTTON
GLO-PLUG
SWITCH
(17,
Figure 4-4-3). The PUSHBUTTON GLO-PLUG switch is
pressed to energize the glow plug in the engines air
intake when ambient air is minus 50F (-150C) or below.
This will preheat the intake air prior to the air entering the
combustion chambers.
4-29
INDICATOR GLO-PLUG (18, Figure 4-3). The
INDICATOR GLO-PLUG (13) is connected in series with
the glo plug in the engine air intake. When the PUSH-
BUTTON GLO-PLUG is pressed the INDICATOR GLO-
PLUG (17) will heat-up and glow red to indicate that the
glow plug is operating.
4-30.
Air Cooler Doors (19, Figure 4-3). The air cooler
doors (26 and 30) control the amount of air being drawn
through the air cooler by the fan. The doors may be
adjusted by closing, opening, and sliding to either side
for cold weather operation.
4-31.
EXTRA FUEL BUTTON (20, Figure 4-3). By
pulling and releasing the extra fuel button, extra fuel is
injected into the engine for easier starting in cold
weather.
4-32.
OPERATION INSTRUCTIONS.
4-33.
PRIOR TO OPERATION. Prior to operation of
the air compressor unit, perform the following procedure:
CAUTION
The unit should be located in an area as
free of dust and dirt as possible. A
highly contaminated atmosphere places
abnormal load on the air cleaners, oil
filters, dehydrators, and compressor,
which
can
result
in
increased
maintenance.
a.
Transport the unit to work site and select a
location as nearly level as possible. Out-of-level shall
not exceed 150 in any direction.
b.
Perform
all
inspection,
checks,
and
services, as required, refer to table 5-2.
c.
Open air cooler doors.
WARNING
Under no circumstances should the air
purification cartridges in cylinders No. 3,
4 and 5 (23, 24, 25, Figure 8-2) be
allowed to become contaminated with
moisture. If in doubt, change the
cartridges.
NOTE
When dehydrator and air purification
cartridges are changed, make certain to
record
hourmeter
readings.
Approximate time elapse for cartridge
change is as follows. Actual frequency
of
cartridge
change
depends
on
governing weather conditions at a given
time or place:
Dehydrators:
Approximate hours
Cylinders 1 and 2
8 hrs.
Air purification
Cylinders
Cylinders 3, 4, & 5
96 hrs.
d.
Check the number of hours that the
cartridges in the dehydrators and filters have been used.
This is done by comparing the time of their installation
with the HOUR-METER (1, Figure 4-2) indication. If the
next period of
4-6
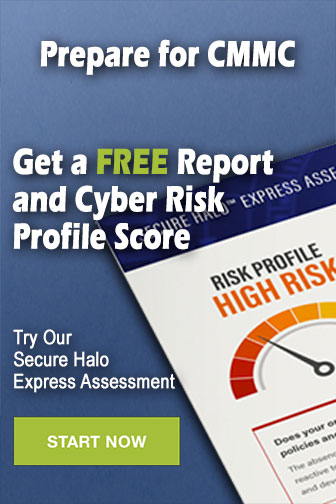