strainer, and through the first stage trap to the
condensate receiver. When pressurized air from the
third compression stage cylinder passes through the
third stage trap it generates a pressure differential in the
third stage trap continuous bleed valve, 900 ± 50 psig
(6201 ± 344.5 kPa) downstream of the valve and 14.7
psi (101.3 kPa) upstream of the valve. The third stage
continuous bleed valve will open, causing the first and
second stage traps continuous bleed valves to open.
This will allow a small amount of moisture laden
pressurized air to bleed off through the third stage trap
filter and line strainer through the first and second stage
traps to the condensate receiver.
4-6.
AUTOMATIC CONTROL AND DRAIN SYSTEM
(See Figure 4-2). A constant speed type unloader is
provided to automatically unload the compressor unit
when the discharge pressure exceeds 3300 psi ± 175 psi
and to load the compressor when discharge pressure
drops approximately 300 psi below unload pressure.
The compressor unit unloads automatically upon
stopping so that the compressor will be unloaded at
startup to decrease the starting load. Upon unloading,
the mechanical filter (figure 5-6) is automatically drained
of condensed moisture and oil. A manual compressor
unload switch is provided on the instrument panel and a
manual control for draining the mechanical filter. When
pressure in the system reaches approximately 3300
±175 psi, the normally closed contacts of pressure switch
(10, Figure 7-2) will open. The solenoid valve (10) is
then deenergized allowing air to flow through the auto
check valve from the second stage to automatic drain
valve, which then opens. The air and condensate in the
mechanical filter exhausts to atmosphere through the
drain
valve
and
into
the
condensate
receiver.
Condensate and a small amount of air is continuously
passed from the third stage trap through line filter and
continuous bleed valve. Likewise, condensate and small
amount of air passes from second and first stage traps
through line filters; through continuous bleed valves, and
is exhausted through the condensate receiver (26).
Condensate passing through the drain valve is collected
in the condensate receiver when the compressor
unloads, actuating the drain valve. Opening the
dehydrator bleed valve (Figure 42), located on the
control panel, will actuate the auto drain valve and
exhaust condensate and air from the dehydrators and
from the accumulator into the condensate receiver. The
intake of the first stage is not closed and will continue to
draw in air but will not compress as the air is allowed to
escape throug through the traps. When system air
pressure drops to approximately 3000 psi, the pressure
switch closes energizing solenoid valve (10, Figure 7-2)
and exhausts the air from automatic drain valve. This
allows the drain valve to close and air being drawn into
the first stage is compressed and the compressing cycle
begins again. A manual drain valve is provided on the
condensate receiver for manually draining
the receiver of condensate moisture. The condensate
receiver shall be drained after every eight (8) hours of
operation or after compressor shut-down.
4-7.
Engine oil pressure switch (12, Figure 7-2) is
connected
to
the
engine
oil
pressure
system.
Compressor assembly oil pressure switch (8) is
connected to the compressor assembly oil pressure
system. The engine oil pressure switch will open and
cause the compressor to unload and engine to stop if oil
pressure is list while the engine is operating. Safety
control relay (10) in the unloader control box is also
deenergized if either oil pressure switch opens. When
the COMPRESSOR UNLOADER switch (7) is in the
UNLOAD position there is no current flow through
solenoid valve (10) and the compressor is unloaded.
When engine and compressor assembly oil pressure
develop after engaging the clutch, the oil pressure
switches close. Switch (7) is placed to the LOAD
position energizing the solenoid valve coil (10). Current
flows through the closed contacts of pressure switch
(10), and the compressor unit will begin to load.
4-8.
ELECTRICAL SYSTEM (Figure 7-2). The air
compressor unit has a 12 volt dc negative ground
electrical system. The electrical system consists of two
primary circuits: starting and charging circuit and pilot
control circuit. The starting and charging circuit starts
the diesel engine assembly and charges battery (1)
during air compressor unit operation. When MASTER
SWITCH (5) is closed, pressing START SWITCH (4)
completes the circuit path for starting motor (2). Voltage
is applied from the positive terminal of (1) across closed
contacts of (5) and (4), (2) solenoid and field coils of (2)
to ground. Simultaneously, 12 volts dc is applied across
AMMETER
(6),
UNLOAD
position
contacts
of
COMPRESSOR UNLOADER switch (7) and coil of
safety relay (10). Relay (10) energizes causing fuel
shutoff solenoid (13) to deenergize. This will shut off oil
fuel from the engine's fuel pump to the injectors. Motor
(2) will turn the engine crankshaft until the engine's oil
pump develops eight psi oil pressure. At eight psig (55
kPa) engine oil pressure, engine oil pressure switch (12)
will open deenergizing safety control relay (10). When
(10) deenergizes, (13) will energize allowing the engine's
fuel pump to deliver fuel to the injectors. This will cause
the air and fuel mixture in the engine cylinders to ignite.
Once the engine is running start switch (4) is released.
Battery (1) is charged by alternator (3) with voltage
regulator controlling the rate of charge. Electrical power
for air compressor unit operation is now supplied by the
alternator (2).
4-9.
Hourmeter (16, Figure 7-2) monitors the running
time of the air compressor unit under load conditions.
When pressure in the system reaches approximately
3200 ± 100 psig (21984 kPa), pressure switch (10) is
opened by
4-3
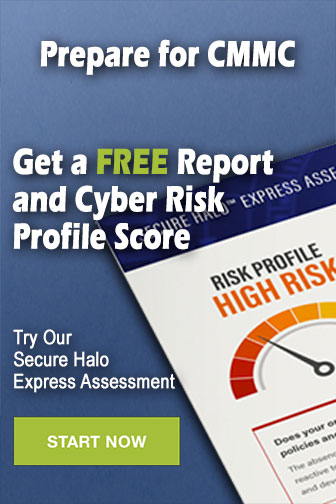