position pump element (9) at its
lowest position.
(e)
Replace delivery valve (7) and copper
gasket (6) in the injection pump.
Screw tool No. 8, adjusting tool for
injection pump, into injection pump.
Attach threaded pin to timing gauge
(tool No. 9) and insert timing gauge
into base mount Adjust gauge for 1
mm of pretension and secure gauge
to base mount. Check gauge for free
movement.
NOTE
After fuel line is attached to injection pump, fuel should
start to flow from the overflow tube on adjusting tool base
(tool No. 8).
(f)
Attach fuel line (73) to injection pump
(34). Turn flywheel counterclockwise
until fuel stops flowing from the
overflow tube. Slowly turn the flywheel
further until fuel starts to emerge very
slightly from the overflow tube. This is
the delivery end. The degree marks
on the flywheel before top dead center
(TDC) must correspond to 120 ± 0.5.
(g)
If
the
degree
readings
do
not
correspond, adjust injection pump (34)
using shims (35). Add shims - delivery
end delayed. Subtract shims - delivery
end advanced. To obtain the exact
thickness of shim (add or subtract).
Set dial gauge of tool No. 9 to 0
where it was determined the engine
was at the "delivery end." See
paragraph (f) above. Turn flywheel
until required degree mark is obtained
(120 ± 0.5). The indicated difference
on the dial gauge is the thickness of
the shims that need to be added or
subtracted to obtain a properly timed
engine.
NOTE
If the fuel emerges slightly from the overflow tube of tool
No. 8, when the correct degree reading (120 + 0.5) on
the flywheel is reached, then correct engine timing for the
delivery end has been obtained.
(h)
Adjustment- Extra Fuel Device (66,
Figure 8-30, Sheet 6 of 10). At the
correct degree reading (120 0.5) and
delivery end setting
reset the dial gauge on tool No. 9 to
"O." Turn the flywheel in a clockwise
rotation until the gauge reading (1.22
mm) is reached. Maintain the
flywheel in this posi-tion. Fuel should
start to flow from the overflow pipe on
tool No. 8. If it does not, use tool No.
10, socket wrench, for extra fuel
button. Adjust extra fuel button until
fuel emerges from overflow tube.
Tighten threaded pins (on top of
crankcase) to se-cure the position of
the extra fuel device, thread pins with
safety wire and seal the wire.
(53) To bleed the fuel system, proceed as
follows:
NOTE
Bleeding of the fuel system should be carried out in two
(2) steps.
(a)
Prime system with hand lever on fuel
feed pump. As the lever is pumped
slowly, loosen bleed screw on top of
the fuel filter a little at a time. Fuel
should emerge from the bleed screw,
bubble free. At this point, tighten
bleed screw.
CAUTION
Do not allow engine to start.
(b)
Loosen the nuts (a couple of threads
only), on fuel lines 1 and 2 at the
injectors, turn the engine over (do not
start engine) until fuel emerges and is
free of air bubbles. Re-tighten fuel line
nuts at injectors and torque nuts to 30
ft-lbs (40 Nm).
6-34. STARTER MOTOR ASSEMBLY (See Figure 8-
31). The following paragraphs contain disassembly,
cleaning, inspection, repair or replacement, and
assembly instructions for the starter motor assembly.
a.
Disassembly. Disassemble the starter motor
assem-bly only to the extent necessary to repair
or replace a de-fective part or parts.
(1)
Unscrew and remove one hex nut (2) and
lock washer (3) attaching field winding (32),
termi-nal lug to bottom solenoid (1),
terminal stud. Remove winding (32) lug
from solenoid (1).
6-52
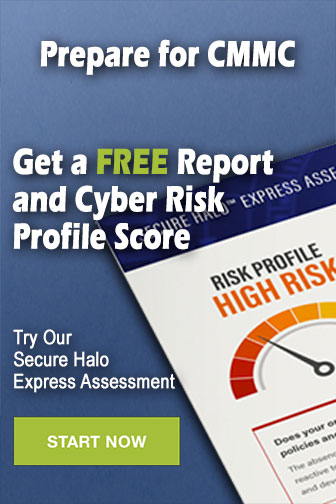