NOTE
Connecting rods (17) should be mounted so that the
identification numbers on the rod halves point to the
blower side of the engine.
NOTE
Apply clean oil to threads and bottom of screw head of
screws (14) before torquing screws.
NOTE
insure that the small valve recess in the piston (9) head
points to the flywheel end of the engine.
NOTE
A piston ring kit is available, replace all piston rings if any
ring needs replacement.
(23) Using a ring spreader (Tool No. 22, Figure
2-1). Install oil control ring (13), stepped
scrapper ring (12), compression ring (11),
and wedge type ring (10) on pistons (9).
Place retainer ring (7) in groove in piston
(9). Attach piston (9) to connecting rod (17)
with piston pin (8). Install retaining ring (7)
in piston (9).
NOTE
Before cylinder (4) is installed, position ring gaps 90°
apart.
(24) If cylinder studs (6) had been removed,
install in crankcase. Using tool No. 23,
piston ring clamp, carefully install cylinders
(4) over pistons (9).
(25) Figure 8-30, Sheet 6 of 10. Place o-ring
(61) over cap (57), install disc (60), pin (59),
and spring (58) in cap (57), install ball (62).
Install in crankcase. Install washer (65) o-
ring 64 on sieve (63). Screw sieve into side
of crankcase.
NOTE
The wider machined side of the table guide plate (37)
should be mounted closest to the cylinders.
(26) Figure 8-30, Sheet 7 of 10. If studs (39)
were removed, Install into crankcase.
Place gasket (38) and tube guide plate (37)
over studs (39). Secure with nuts (36).
NOTE
New valve guides (49) shall be reamed out us-Ing valve
guide reamer (tool No.36, figure 2-1).
(27) If valve guides (49) were removed from
cylinder head (50) press in new valve
guides (49) using Tool No. 20, valve guide
insertion tool. Mini-mum insertion force
required 220 lbs.) Insert valves (48, 47) in
head (50). Using Tool No. 21, punch, seal
cap, install seal caps (46), large washer
(45), small washer (44), internal and
external springs (43, 42), spring clip (41 )
and lock covers (40). Apply a light coat of
sealing com-pound, Military Specification,
MIL-S46163 or equal to threads of studs
(25). Install studs (25), bracket (24) and
secure with nuts (14). Torque collar nuts
(14) to 33 lb-ft (45 Nm).
NOTE
Use only one gasket (51) of correct thickness per
cylinder.
(28) Using cylinder clamp (Tool No. 37, Figure
2-1) clamp cylinder so that it is stationary
when flywheel is turned over. Place timing
gauge clamp (Tool No. 16) on measuring
bridge (Tool No. 17); place the measuring
bridge on a flat plate and insert timing
gauge (Tool No. 9) into clamp. When
gauge shows 3 ro 4 mm pre-tension, clamp
gauge in place. Place measuring bridge
with clamp and gauge on top of cylinder.
Check dimension between piston at TDC
(top dead center) and top of cylinder head.
Correct bumping clearance is 0.043 to
0.051 inches (1.1 to 1.3 mm). Total
thickness of the gasket (51) and distance
between piston and top of cylinder should
equal bumping clearance tolerances.
CAUTION
Make sure that push rod tubes (31) are properly seated
when assembled.
(29) Lightly grease gasket (51) and place on top
of cylinder. Place o-ring (34), pressure ring
(33), spring (32) and tubes (31) into tube
guide plate (37). Place o-ring (34),
intermediate ring (35) in cylinder head (50).
Install cylinder head (50) over studs and
position tubes (31) into recesses in cylinder
head (50). Install exhaust manifold studs
(30) in cylinder heads (50).
NOTE
Prior to torquing cylinder head nuts, tighten enough to
where cylinder heads are still moveable. Fit the exhaust
manifold (28) to the cylinder heads. This correctly
positions the cylinder heads. Tighten and torque cylinder
head nuts as noted.
6-48
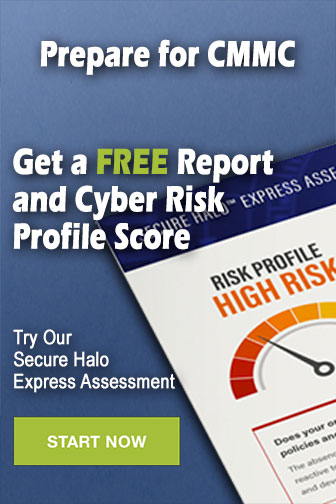