(4)
Using tool No. 25, camshaft bearing punch
(Figure 2-1), install camshaft bearings (62,
62a, Figure 8-30, Sheet 7 of 10). Install
cover (63) using tool No. 30, mounting tool
for main bearing (gov. end), install main
bearing (22a, Figure 8-30, Sheet 4 of 10).
(5)
Install counterweights (43) onto crankshaft
(45) using washers (42) and screws (41).
Torque screws (41) to 81 ft-lbs (110 Nm).
Mount crankshaft bearings (39) into bearing
support holes (38b). Align oil hole and
attach bearing halves to crankshaft (45)
using screws (37). Torque to 81 lbs-ft (110
Nm).
(6)
Insert
crankshaft
(45)
into
crankcase.
Attach bearing support (38b) to crankcase
using wash-ers (38a) and screws (38).
Torque screws (38) 81 lbs-ft (110 Nm).
(7)
Install crankshaft bearing (35) into bearing
flange (28) using tool No. 29, mounting tool
for main bearing (flywheel end). Press in oil
seal ring (34) using tool No. 28, oil seal
punch bear-ing flange. If studs (30) were
removed, install studs (30), gasket (29),
bearing flange (28), washer (27) and nuts
(29). Check end play of crankshaft (0.2
mm - 0.7 mm). If the tolerance does not
check correctly, remove the bearing flange
(28) and insert the proper size shim (31).
Reinstall bearing flange and torque nuts
(26) to 36 lbs-ft (50 Nm).
(8)
Fit bushing (25) in proper hole in end of
crank-shaft (45). Install buffer ring (32).
Match fly-wheel hub (24) to bushing (25)
and attach fly-wheel hub (24) to crankshaft
(45) using screws (23). Torque screws (23)
to 103 lb-ft(140 Nm).
(9)
Figure 8-30, Sheet 5 of 10. Using screws
(19),
attach
engine
flange
(20)
to
crankcase. If gear ring (18) was removed
from flywheel (17), heat gear ring evenly all
around circumference to 300-350°F (1490C
+ 1770C). Place gear ring onto flywheel
tapping gently to place gear ring as needed.
(10) Install flywheel (17) to flywheel hub using
alignment pin to assure proper flywheel (17)
positioning and attach using screws (16).
Torque screws (16) to 107 lb-ft (145 Nm).
(11) Figure 8-30, Sheet 3 of 10. Install o-ring
(53) onto throttle shaft (52). Insert throttle
shaft
(52) into crankcase, positioning the slot in
shaft toward the non-drive end of the
crankcase. Attach spring (54) to throttle
shaft (52). Posi-tion lever spring (55a) onto
the shaft of the connecting lever (55).
Install the governor lever (58) onto the
connecting lever (55) and secure with
retaining ring (55b). Apply clockwise
tension to spring (55b) by rotating governor
lever
over
full
revolution.
Position
connecting lever (55) onto shaft (52) and
secure by installing pin (51). Connecting
lever (55) must be easily moveable, after
installation.
(12) Insert control rod (59) through side of
crank-case. Install support (62) and
support guide (61) using lockwashers (61)
and screws (60). Position control rod (59)
on guide support (61). Attach governor
lever (58) to control rod (59) and secure
with retaining clip (57). Attach spring (56)
to support (62) and control rod (59).
NOTE
Tension adjustments on throttle shaft move-ment can be
made by the adding or subtract-ing of shims (42).
(13) Install locknuts (50) on screws (49); install
screws (49) into side of crankcase next to
throttle shaft (52). Be sure slot on throttle
shaft is toward the non-drive end of the
crank-case. Do not tighten adjusting
screws at this time. Install shims (44),
spacers (45), tension plate (47) and screws
(43). Attach throttle lever (42) to throttle
shaft (52) using lockwashers (41) and
screws (40). Throttle lever (42) should
point of the downward position when
installed correctly.
(14) Figure 8-30, Sheet 6 of 10. Install o-ring
(67) onto extra fuel device (66). Using
socket wrench (Tool No. 10, Figure 2-1)
screw extra fuel device (66) into crankcase.
(15) Figure 8-30. Sheet 7 of 10. To assemble
the governor onto the camshaft proceed as
follows:
(a)
Position gear wheel (66) so that the
face stamped with "0/15°" is facing
outward. Attach the camshaft (68),
gear wheel (66) and starter sleeve
(63)
with
lockwashers
(62)
and
screws (61). Do not tighten screws
(61) at this time. Install pin (67)
6-46
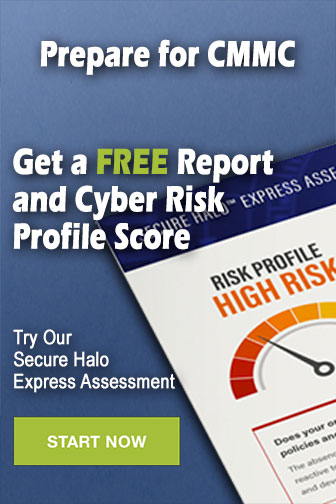