NOTE
Care should be taken to assure that spring (45) is not
lost when breather cover (43) is removed.
(45) Figure 8-30, Sheet 6 of 10. Unscrew and
re-move
nut
(41)
and
washer
(42).
Disengage breather cover from crankcase
and lift off stud (51). Remove spring (45),
plate (46), diaphragm (47), valve breather
plate (48), screen (49), intermediate plate
(50), stud (51) and hex nut (52). Oil splash
plate (53) need not be removed unless the
plate is to be replaced. Remove gasket
(44) from cover (43).
(46) Figure 8-30, Sheet 9 of 10. Remove nuts
(34), washers (35) from oil cooler mounting
studs (61) and remove cover panel (36);
remove mounting screws (50). Oil cooler
tubes (54) with oil pipe right (51) and oil
pipe left (53) may be pulled from the
mounting studs (61) as a unit. Remove oil
pipe right (51) and oil pipe left (53) from
tubes (51) and remove o-ring (55) from
each.
Remove
gasket
(52)
from
crankcase. Studs need not be removed
unless repair is necessary.
b.
Cleaning. Refer to paragraph 6-3.a for general
clean-ing instructions.
(1)
Parts that will be repainted may be cleaned
with steam. Avoid use of water or steam on
electrical components and wiring.
(2)
After cleaning, refinish affected painted
areas where required in accordance with
T.O.35-1-3.
(3)
Remove caked grease or dirt with a non-
metallic brush after immersing part in
solvent. Scrape carbon, grease, and old
gasket material from affected surfaces.
(4)
Clean cylinders and pistons with care. Do
not mar
or scratch contact or seating
surfaces. Piston ring grooves must be
cleaned with care so as not to scratch or
mar grooved surfaces.
CAUTION
Do not immerse prelubricated bearings in dry cleaning
solvent prior to installation.
(5)
Clean
bearings
by
immersing them in dry cleaning solvent per
Federal Specification P-D-680, Type II, and
air dry.
c.
Inspection. Refer to paragraph 6-3.b for general
in-spection instructions.
(1)
Parts with dimensions listed in Table 6-1,
Table of Limits shall be measured to
ascertain
accept-ability
for
repair
and
assembly.
(2)
Cylinder head covers (4, Figure 8-30, Sheet
7 of 10) for damaged contact surface.
(3)
Rocker arm bushings (20, Figure 8-30,
Sheet 7 of 10). Refer to Table 6-1.
(4)
Adjusting screws (19) for worn ball heads.
(5)
Rocker arms (17 and 23) for worn radius
(flats). Refer to Table 6-1.
(6)
Shaft on rocker arm brackets (24) for wear.
(7)
Valve springs (42 and 43) for cracks,
breaks and set. Refer to Table 6-2.
(8)
Valve guides (49) for wear. Refer to Table
6-1. Cylinder heads (50) for damaged
contact surfaces.
(9)
Valve seats in cylinder heads (50) to see if
valve seats may be recut. Refer to Table 6-
1.
(10) Cylinder heads (50) for cracks between
valve seats and injector aperture.
(11) Cylinders (4, Figure 8-30, Sheet 4 of 10) for
evidence of piston seizure or scores on the
running surface. Refer to Table 6-1.
(12) Piston ring (10, 11, 12, and 13) sets for
wear.
(13) Pistons (9) for evidence of seizure or
cracks in the area between the ring
grooves.
(14) Piston ring grooves for wear.
(15) Piston pin bushing (16) for wear. Refer to
Table 6-1.
(16) Connecting rods (17) for blue coloration or
incline.
6-44
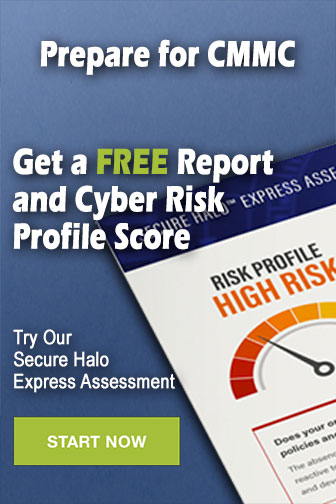