(10) Disconnect and remove service valve to
service hose bleed valve tube assembly
(23). Tag for reassembly reference.
(11) Disconnect and remove tube assembly (17)
at tee (27). Disconnect and remove tube
assembly (5) at tee (31). Tag for
reassembly reference.
(12) For the service hose bleed valve (29),
mechanical filter drain valve (33) and
dehydrator
bleed
valve
(37)
remove
handles, unscrew and remove lock nuts,
and remove the valves from panel (44)
from the rear.
(13) Remove retaining nut and flat washer (40)
from unloader switch (39). Remove switch
(39) from panel (44) from the rear.
(14) Loosen adjusting nut at the back of the
panel on push button (42). Unscrew and
remove top cap from push button (42).
Remove the push button from the back of
the panel.
(15)Unscrew and remove the cover of indicator
(43). Remove indicator (43) from the back
of the panel.
b.
Cleaning. Refer to paragraph 6-3.a. for general
cleaning instructions.
(1)
Clean all unpainted metal parts using
cleaning solvent that is in accordance with
Federal Specification P-D-80, Type II, or
equivalent. Wipe nonmetallic parts with a
clean, lint-free cloth moistened in detergent
and water and air dry.
(2)
Clean all painted surfaces by spraying with
hot water and detergent solution per
Federal Specification P-D-220. Parts that
will be repainted may be cleaned with
steam. Avoid use of water or steam on
instruments, electrical components and
wiring. After cleaning, refinish affected
painted
areas
where
required
in
accordance with T.O.35-1-3.
(3)
Wash glass gauge faces with a soft cloth
and warm soapy water or equivalent. Dry
with a clean lint-free cloth. Use care not to
damage indicators.
Proper precautions must be exercised to protect
personnel. Stand clear of all tubing openings.
After cleaning, drain tubes, and dry with
low pressure compressed air (30 psig 1207
k Pa] maximum).
(4)
Clean outside and inside surfaces of steel
tubing assemblies with compressed air,
pressurized hot water and detergent or
steam.
Do not use steam or water to clean any electrical
components or assemblies such as switches,
starter motors, or solenoids.
(5)
To
clean
electrical
components
use
trichloroethane, per Federal Specification
O-T.620. or equivalent, and air dry parts
thoroughly.
c.
Inspection. Refer to paragraph 6-3.b for general
inspection procedures.
(1)
Tubing for cracks, chaffing, deformation or
wear.
(2)
Hexagon nuts for stripped or damaged
threads.
(3)
Screws for stripped or damaged threads.
(4)
Threaded parts (fittings, etc.) for stripped or
damaged threads.
(5)
Rubber grommets for cracks, excessive
wear or deformation.
d.
Repair or Replacement. Refer to paragraph 6-
3.for general repair or replacement procedures.
(1)
Replace damaged or defective nipples.
couplings and gauges.
(2)
Replace all threaded parts having worn,
stripped, or damaged threads.
(3)
Replace damaged or defective tubing.
(4)
Replace damaged or defective fittings.
(5)
Replace damaged or defective pressure
switch.
(6)
Replace damaged or defective lamps,
switches or switch assemblies.
(7)
Replace identification plates if marking are
illegible.
6-13
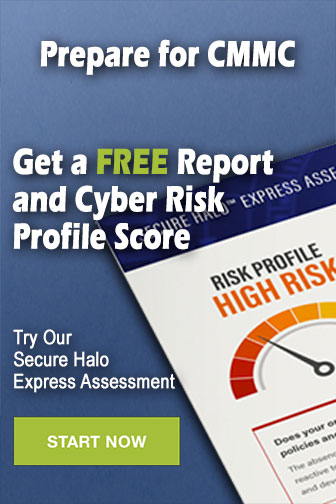