1st stage valve ..........
80 psig( 552 kPa)
2nd stage valve .........
240 psig ( 1,655 kPa)
3rd stage valve ..........
1,500 psig (10,343 kPa)
4th stage valve ..........
3,800 psig (26,196 kPa)
(b)
If safety valve relieves pressure prior
to or after specified pressure.
replace safety valve.
(2)
Screw a steel pipe plug into first stage
outlet opening. Pressurize air cooler with
low pressure air (30 psig [207 kPa]
maximum) at first stage inlet opening.
Immerse cooler first stage in water.
Inspect for any leaks.
(3)
Remove pipe plug and air source from
first stage. Repeat step (1.) (a.) for
second, third, and fourth stages of air
cooler.
(4)
Refer to REPAIR OR RLEPLACEMENT
to repair leaks in the air cooler.
d.
Repair or Replacement. Refer to paragraph 6-
3.c. for general Repair or Replacement instructions:
(1)
Replace all threaded parts having worn,
stripped. or damaged threads.
(2)
Replace damaged o, detective fittings.
(3)
Replace damaged or defective safety
valves.
(4)
Straighten bent or dented shroud
assembly. Weld any cracks or breaks.
(5)
Repair air cooler, if leaking, as follows.
(a)
Using an oxy-acetylene torch,
carefully unsolder U-bend end fitting
on stub from one end of the
defective tube.
(b)
Manufacture extraction tool by using
a four inch long 0. inch diameter
(102 mm long, 9.525 mm diameter)
solid steel rod. Solder a three inch
(7.63 mm) piece of same material
for t-handle. Insert tool into exposed
elbow end, flared end of the
defective tube, work the defective
tube loose from the cooling fins.
(c)
Rotate the tool installed in step 2,
but do not exert extreme that will
deform tube. If tube will not work
loose, use a i6-16 blade type screw
driver or other flat tool to work each
cooling fin gently back and forth to
relieve any oxide or corrosion.
Spray the tube around the fins with
silicone lubricant (NSN 9150-00-
823-78060).
(d)
Manufacture a new tube section and
have one end swaged to proper size
for resoldering of end piece.
NOTE
Use a piece of asbestos cloth or other
heat shield to protect surrounding fittings
from direct flame. Small pin holes can
develop in the solder joints of existing
fittings if they are not protected.
(e)
Ensure ends of new tube, original
fittings, and all unsoldered areas are
clean. Insert new tube through
cooler. Use silver solder and flux,
resolder new tube and original
fittings back into place.
(f)
After soldering is finished, test the
cooler with low pressure air and
water, refer to INSPECTION to
determine if any leaks are present. If
leaks are present, resolder where
necessary. Check the cooling
stages to the proper pressure for
each with water or hydraulic
pressure. If hydraulic pressure is
used, be sure the tubes are purged
of hydraulic fluid before repainting
and re-use.
e.
Assembly. To assemble the air cooler group,
proceed as follows:
(1)
Using six screws (23) attach fan shroud
(24) to (cooler (25).
(2)
Assemble elbows (22, 21), tee (20) to
cooler (25). Assemble adapter (19) and
safety valve (18) to tee (20).
(3)
Assemble elbow (17) to cooler (25),
assemble tee (16) to elbow (17) and
elbow (15) and safety valve (14) to tee
(16).
(4)
On the opposite side of the cooler
assembly, install tubing adapter (13), tee
(12) and tubing elbow (11). Assemble
safety valve (10) with tee (12).
(5)
Assemble street tee (9), tubing elbow
(8), reducing bushing (7) and safety
valve (6).
(6)
Using washers (4, 3, and 2), attach
guard (5) it, shroud (24) using (1)
6-16
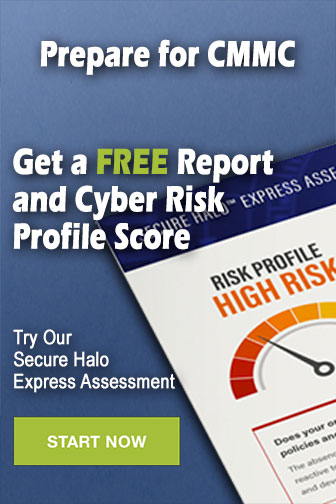