(5)
Replace pistons and piston pins not
meeting the tolerances given in Table 6-1
(Table of Limits).
(6)
Replace all damaged piston rings.
The connecting rod bearings shall be
replaced, regardless of apparent
condition, at the end of each 10,000-
hour operating period.
(7) Replace oil pump blades if blades are
worn, chipped, cracked or broken.
Replace entire oil pump if parts other than
blades require replacement.
(8)
Replace damaged or defective oil strainer.
(9)
Replace end covers if worn, cracked,
chipped, or warped. Remove minor burrs
with a fine hand stone.
(10)
Replace crankshaft bearings if worn,
scored, or damaged in any way that will
impair their normal function.
(11)
Replace crankshaft having worn, scored,
pitted, or out of round journal or bearing
surfaces, permanently restricted oil
passages, and if tolerances given in Table
6-1 (Table of Limits) are not met.
(12)
Replace crankcase if cracked or if mating
surfaces are damaged or warped.
NOTE
Minor nicks, scratches, and burrs may
be honed with a fine hand stone.
(13)
Replace any defective cylinder.
e.
Assembly. To assemble the air compressor
assembly, proceed as follows:
Do not mount oil sump (121) in a vise.
NOTE
A compressor overhaul kit consisting of
all gaskets, o-ring, and oil seals is
available. Replace all gaskets, seals,
and o-rings, coat gaskets and o-rings
with a light coat of petrolatum, per
Federal Specification VV-P-236, to aid in
assembly.
(1)
Mount the oil sump (121) in a suitable
holding fixture to start assembly.
Assemble o-ring (124) in groove on sump.
Assemble crankcase (127) to sump (121)
and attach with three lock washers (123)
and screws (122). If removed, attach
serial number plate (125) to crankcase
with screw (126). Assemble oil strainer
(120) in sump.
(2)
If pipe plug (119) was removed from
crankshaft (118) install the pipe plug (119).
Place connecting rods (115, 116, and 117)
in crankcase (127) with rod bearing ends
through crankcase cylinder bores.
(3)
Assemble balance weight (112) to drive
end of crankshaft (118) bearing journal
with lock washers (114) and cap screws
(113).
(4)
Heat drive end bearing (111) by immersing
in oil heated to temperature of 350°F
(177°C). Allow bearing to heat from five to
ten minutes; then, assemble on crankshaft
drive end journal with bearing inner race
against shoulder of balance weight (112)
(5) Assemble a new oil seal (110) in bore of
drive end cover (104) flush with outer face
and with sealing lip facing inward. Press
three dowel pins (77) in end of crankshaft
(118) leaving approximately half of pin
protruding from crankshaft. Carefully
assemble drive end cover (104)
over
bearing (113). Place new gasket (I09)
against end cover (104) flange aligning
holes. Insert non-drive end of crankshaft
(118) through drive end of crankcase and
carefully through the connecting rods (115,
116, 117). Secure drive end cover (104)
to crankcase (127) with lock washers (106,
108), one 1-1/4 inch long cap screw (107)
and five 1-1/2 inch long cap screws (105).
(6) Assemble drive ring gear (76) to flywheel
(79) with lock washers (78) and cap
screws (77). position flywheel gasket (83)
on end of crankshaft over dowel pin (82)
and carefully assemble flywheel (79) to
end of crankshaft (1 18) with three
lockwashers (81) and socket head cap
screws (80).
6-21
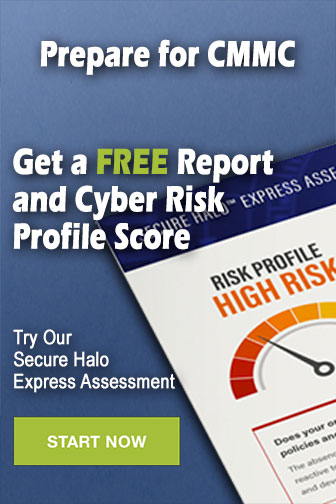