(:3)
Support the crankshaft with suitable
wooden blocks and remove live cap screws (105), one
cap screw (107), lock
washers (106, 108), separate
and remove
drive end cover (104) from crankcase
(127). Remove gasket (109). Press oil seal (110)
out of end cover (104).
(24)
Use a bearing puller, remove the two
crankshaft bearings (111) from each end of crankshaft
(118). Remove two cap screws (113) and lock washers
(114) from each of the two balance weights (112) and
remove the balance weights (112) from crankshaft (118).
(25)
carefully lift crankshaft off supporting
blocks and withdraw from crankcase, removing the
connecting rod assemblies (115. 116, and 117) from
crankshaft journal as crankshaft is being withdrawn. Do
not remove pipe plug (119) from crankshaft (118) except
for cleaning of oil passages. or for replacement because
of leakage,.
(26)
Unscrew and remove oil strainer (120)
from sump (121). Remove three cap screws (122) and
lock washers (123), remove oil sump(121) and o-ring
(124). Do not remove tapping screws (126) and serial
number plate (125) from crankcase (127) unless
replacement of the plate or crankcase is necessary due
to damage. When replacing serial number plate (125).
make certain all data from old plate is stamped on new
to retain same serial number for service records.
b.
Cleaning. Refer to paragraph 6-3.a for general
cleaning requirements.
(1)
Clean all painted surfaces by spraying with
hot water and detergent solution per Federal
Specification P-D-220.
(2)
Parts that will be repainted may be
cleaned with steam. Avoid use of water or steam on
instruments, electrical components, and wiring.
(3)
After cleaning, refinish affected painted
areas where required in accordance with T.O.34-1-3.
(4)
Remove caked grease or dill with a
nonmetallic brush after immersing part in solvent.
Scrape carbon, grease, and old gasket material from
affected surfaces.
(5)
clean compressor cylinders are (id pistons
with care. I)o not liar or scratch contact or seating 6-20
surfaces. Piston ring grooves must be cleaned with care
so as not to scratch or mar grooved surfaces. Use a
section of old piston ring corresponding to groove size
for this purpose.
Do not immerse in dry cleaning solvent prior to
installation.
(6)
Clean bearings by immersing them in dry
cleaning solvent per Federal Specification P-D-680, Type
II, and air dry.
c.
Inspection. Refer to paragraph 6-3.b. for
general inspection requirements. Refer to Table 6-1,
Table of Limits for dimensional inspections.
d.
Repair or Replacement. Refer to paragraph 6-
3.c. for general repair or replacement requirements.
(1)
Replace oil seal, gaskets, and preformed
o-ring packing.
NOTE
Minor nicks, scratches, and burrs may be
honed with a fine hand stone.
(2)
Replace cylinders having cracks, broken
fins, damaged or warped mating surfaces, and if
tolerances given in Table 6-1 (Table of Limits) are not
met.
Do not remove any more material than is
necessary to completely remove the glaze.
Clean the cylinders in accordance with
CLEANING instructions.
(3)
Remove glaze front cylinder walls with
portable cylinder hone (using 280 to 400 grit stones), a
.glaze breaker, or a crocus cloth, depending on condition
of cylinder walls.
(4)
Replace pistons if worn, cracked, scored,
scuffed, and if ring lands are worn or broken.
NOTE
If a piston is found to be detective, replace
piston and piston pin as an assembly.
6-20
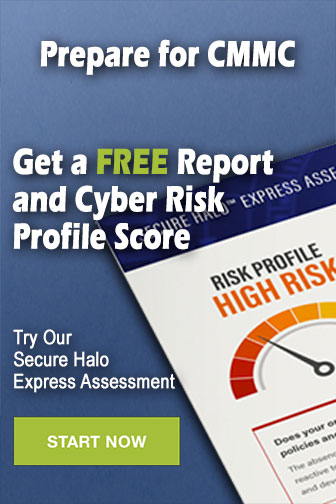