b. The reference input from a Magnetic Pickup mounted
to sense the rotation rate of the helicopter main rotor is
applied through the MAG pickup jacks to operational am-
plifier U101A. The output of U101A is one negative pulse
for each positive input pulse. Generally, there is one pulse
per blade, except one blade will have a double pulse which
is used as a reference. The network between U101A and
U103B produces a positive pulse only for the double pulse
when the cathode of CR102 is grounded by INTERRUPT-
ER LOGIC switch S105. Thus, U103B is triggered at the
one-per-revolution rate of the main rotor.
c. The positive pulse from U103B triggers unijunction
oscillator Q103 and Q104 and resets binary counter U104
and JK flip-flop U105A. The output of oscillator Q 103
and Q104 is applied through driver U103E to the clock
input of the binary counter U104, which counts to 12,
resets, counts to 12, and resets again. The 12-count output
of U104 causes U105A to change state and change the
polarity of integrator driver U102C and integrator U101B.
The integrator output determines the frequency of oscil-
lator Q103 and Q104 so that the counter totals 24 counts
(twice 12) when the next reset command is applied to
U103B. Thus, the oscillator operates at 24 times the ref-
erence input signal.
d. The binary state of counter U104 is applied to quad
latch U106, and the output of flip-flop U105A is applied
to the J and K inputs of JK flip-flop U105B, which also
acts as a latch. The output of latch U106 is responsive
to input signals from the counter only when a positive
sample command from the Balancer is applied through
U103A and U102D to enable the quad latch U106. Thus,
the output of the latch remains in the same state that
appeared at the input at the time of the sample command.
Flip-flop U105B is clocked by the positive sample com-
mand and its output remains in the same state.
e. The output of the quad latch is decoded by decoder-
driver U107 and decoder-drivers U102A, U102B, U103C,
and U103D to light one of the 24 light-emitting diode
(LED) indicators that correspond to the phase relationship
between the one-per-revolution reference input signal and
the vibration signal from the Balancer.
f. TEST switch S1201 removes the one-per-revolution
sample command from the Balancer and substitutes the
reference input signal from the Magnetic Pickup. This
provides one input signal for each blade. The clock dis-
play then is one light for each blade at the same angular
positions as the blades.
4-7. Power Supplies. The Balancer and Phazor have
separate power supplies operating from +28 vdc input
power.
a. The Balance-r power supply provides regulated +9
and -9 vdc for the Balancer circuits. The +9 vdc is provid-
ed by transistors Q104 and Q105 operating as a constant-
current source to zener diode CR115. The -9 vdc is pro-
vided by a high frequency oscillator consisting of transis-
TM 55-4920-402-13&P
tors Q101, Q102, Q103, and coil L101 operating as a
constant-current source to zener diode CR114.
b. The Phazor power supply provides a regulated +5
vdc and +10 vdc for the Phazor circuits. The +5 vdc is
provided by series regulator transistors Q1101 and Q102
(fig. 4-2). The regulated +10 vdc is provided by constant-
current source transistor Q101 and zener diode CR110.
4-8. Strobex.
a. The Strobex (fig. 4-3 and FO-3) contains a point
source, high intensity flash tube (Vl201) fired by an
oscillator operating in one of three modes: slave, locking,
or free-running. As a slave oscillator, it is triggered by
Accelerometer or Magnetic Pickup signals. As a locking
oscillator, the frequency is set to a certain repetition rate
and is synchronized by a one-per-revolution signal from a
Magnetic Pickup. As a free-running oscillator, the fre-
quency is set by a potentiometer calibrated in RPM. The
oscillator is comprised of transistors Q3 and Q4, program-
mable unijunction transistor Q5, and SCR Q6 located on
Blade Tracker Circuit Card C3984.
b. The oscillator is operated in one of five modes of
operation controlled by MODE switch S501B and S50lC.
The following paragraphs (1) through (5), explain each
of the five modes of operation:
(1) Mode A. When set to position A, the Strobex
operates in a slave mode, flashing only when commanded
by the Balancer and is used for main rotor tracking and
tail rotor balancing. The rotating swashplate is fitted with
two interrupters (one of which is double, because of the
Phazor). When the Balancer is set to TRACK, the Strobex
will flash twice-per-revolution, illuminating each of the
two blade tips when they pass the front of the helicopter
(and also when they pass over the tail boom). Thus, the
two Tip Targets will be seen, superimposed, at the front
of the helicopter. (They can also be seen over the tail
boom, but this is not useful except for ground tracking.)
Since one Tip Target has a reflective horizontal bar, and
the other has a vertical bar, the judgement of track is
simple. The Reflective Targets face inboard so they are
viewed from the cabin, either on the ground or in-flight.
When an Accelerometer is secured on the tail rotor gear
box and connected to the Channel B input, the Balancer
is switched to Mode B, and the Strobex will flash once-
per-revolution in response to the vibration signal induced
by the out-of-balance rotor. When a Reflective Target,
secured to the rotor hub, is viewed from a distance with
the Strobex, the target will appear stopped at some angle.
This is the clock angle to be entered on the Balance. Chart
and will tell where to change weight.
(2) Mode B. Position B is rdso used for main
rotor tracking where higher intensity light is required.
The unique locking oscillator of position B is typically
used for the larger rotors with four or more blades. In
those cases, only one single interrupter is secured to the
rotating swashplate and the oscillator causes the Strobex
to flash for the other blades. By fine adjustment of the
4-5
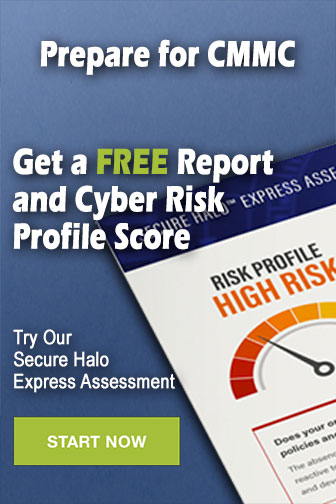