Do not use steam or water to clean any
electrical components or assemblies such
as electrical gauges, switches and solenoids
(3)
Clean electrical components with trichloro-
ethane, per Federal Specification O-T-620
or equivalent.
Proper precautions must be exercised to
protect personnel. Stand clear of all tubing
openings. After cleaning, drain tubes, and
dry with low pressure compressed air (30
psig maximum [206 kPa]).
(4)
Clean outside and inside surfaces of the
steel tubing and hose assemblies with
compressed air, pressurized hot water and
detergent or steam
b.
Inspection. In general, inspect as follows
(1)
Inspect for visible wear, damage, distortion,
cracks, breaks, and corrosion. Replace all
o-rings, gaskets and seals.
(2)
Inspect threaded parts and hardware for
stripped threads, cross-threading and for
nicks and burrs.
(3)
Inspect flex hoses and tubing for evidence
of
leaks,
cracks,
pinching,
chaffing
conditions, damaged connecting nuts, and
similar defects
(4)
Inspect
painted
surfaces
for
chipping,
peeling or discolored paint.
c.
Repair or Replacement. For the most part,
repair of this equipment will be made by replacement of
worn
or
damaged
parts.
Detailed
repair
and
replacement procedures for specific parts are found in
the following subassembly paragraphs.
(1)
Minor nicks, scoring or scratches on non-
critical surfaces may be smoothed with
crocus cloth per Federal Specification PC-
458
(2)
Repair or replace damaged or defective
steel tubing. To repair or replace steel tube
assemblies attachment fittings, proceed as
follows:
NOTE
Before attempting to repair tube fittings, make certain
stainless steel tubing is of sufficient length to fit after
cutting off end containing damaged fittings If not long
enough, replace while tube assembly.
(a)
Cut off tubing just beyond damaged
fitting
(b)
Slide tubing nut and then the sleeve
onto the tubing, refer to Figure 6-1. Make certain end of
tubing is free of any burrs and is reasonably square.
(c)
Insert the end of the tubing into mating
fitting, see Figure 6-2. Make certain that tubing end is
bottomed on fitting shoulder Apply a good grade of
lubricant on end of tubing.
(d)
Turn tubing nut slowly with wrench
while turning tubing with other hand. When the sleeve
grips the tubing, that Is when the tubing can no longer be
turned by hand, stop turning nut and note position of
wrench. This is termed the nng grip point
(e)
Then, tighten the nut an additional one
turn past the ring gnp point.
(f)
Unscrew nut and remove the tubing
from the mating fitting, or presetting tool Inspect the
preset as described in Figure 6-1.
(g)
When
installing
a
preset
tubing
assembly, lubricate the threads and seat of the fitting
and the shoulder of the sleeve with a small amount of
good grade lubricant such as clean compressor oil.
At installation of tubing assembles, do not
overtighten tubing nuts.
(h)
Insert tubing assembly into fitting and
tighten nut until a sharp use in torque is felt Starting at
position of sharp torque rise, tighten the nut 1/4
additional turn to complete the assembly.
6-2
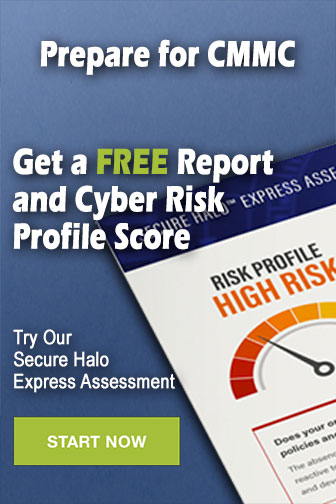