brakes release at a maximum of 65 psi trailer supply
(emergency) line pressure as the trailer air brake
system is recharged to full operating pressure.
5.
With tractor and trailer air brake systems fully
charged, stop engine Reduce pressure by making a
series of foot valve applications, and note that trailer
brakes apply automatically at approximately 20 psi,
tractor reservoir pressure or at the automatic
emergency setting of the tractor protection
equipment, if installed.
If the valve does not function as described, or if leakage
is excessive, it is recommended that it be replaced with a
new or remanufactured unit or repaired with genuine
Bendix parts available at Bendix HVSG outlets.
REMOVING AND INSTALLING
REMOVING
1.
Block trailer wheels.
2.
Drain trailer system air reservoirs.
3.
Identify and disconnect air lines from valve.
(Note: the emergency piston and valve assembly,
generally referred to as the "insert" can be removed
without line removal. To remove the insert, remove
the exhaust cover and pull insert out.)
4.
Remove mounting bolts, or unscrew from pipe nipple
mount
INSTALLING
If valve will be flange mounted directly to steel, it is -
recommended that a flange gasket be utilized to prevent
electrolytic action between the unlike metals. If the valve
is adapter or nipple mounted directly to a reservoir, it is
recommended that "Never Seez" lubricant be applied to
the threads before installation. This will prevent galling
of the threads and make removal easier.
1.
Clean and inspect all connecting line and hoses for
cracks, deterioration or damage. Replace as
necessary.
2.
Mount valve securely
3.
Connect all lines and hoses to valve
DISASSEMBLY (Ref. Figure 4)
1.
Mark cover (1) and body (9) to assure proper
positioning when assembling.
2.
Remove cap screws (27), lockwashers (26) and
exhaust cover (25).
3.
Remove check valve (20) and check valve spring
(21) and O-Rings (22 & 24). Remove spring (23).
4.
Remove exhaust diaphragm screw (30), diaphragm
(28), and washer (29) from exhaust cover.
5.
Remove cap screws and lockwashers from cover (1)
6.
Remove cover (1), relay piston (3) and piston return
spring (5) (if so equipped). Remove piston O-Ring
(2). Remove O-Ring (8) from body bore.
7.
Remove exhaust valve seat (4) from piston.
8.
Remove sealing ring (6) from body
9.
Remove filter assembly (7) from emergency (supply)
port. (Note: If new insert is to be installed, omit steps
10-1 5.)
10. Apply downward pressure on emergency piston (11)
and remove emergency piston and inlet/exhaust
valve assembly.
11. With Tru-Arc pliers, remove large valve retainer (19)
from bottom of emergency piston assembly.
12. Push through small end of emergency piston (11)
with finger and remove inlet/exhaust valve assembly
13. Remove emergency piston O-Ring (10) and O-Ring
(15) from inlet/exhaust valve assembly.
14. Remove retaining ring (18) from inlet/exhaust valve
assembly.
15. Remove valve guide (17), spring (14), retainer (13)
and valve guide O-Ring (16).
CLEANING AND INSPECTION OF PARTS
Wash all metal parts in mineral spirits.
Wipe rubber parts dry.
Inspect all parts for wear, damage or deterioration.
Clean or replace all filters.
Replace all rubber parts and any other part not
considered serviceable by these inspections.
ASSEMBLY (Ref. Figure 4)
Note All torque specified are assembly torque and can
be expected to fall off after assembly. Do not re-torque
after initial assembly torque fall. For assembly, hand
wrenches are recommended.
Prior to assembly, lubricate all O-Rings and mating
surfaces with Dow-Corning 55-M pneumatic grease
(Bendix Pc. No. 291126). (Note: If new insert is
installed, omit steps 1-6.)
1.
Install O-Ring (16) in valve guide (17)
2.
Install valve retainer (13), spring (14) and valve guide
(17) to inlet/exhaust valve.
3.
Compress spring by holding valve guide and install
retaining ring (19). Make certain the ring is properly
installed in groove.
4.
Install O-Ring (15) on valve guide.
5.
Install inlet/exhaust valve assembly into emergency
piston. With Tru-Arc pliers, install valve retainer (19)
making certain it Is in groove.
8-7
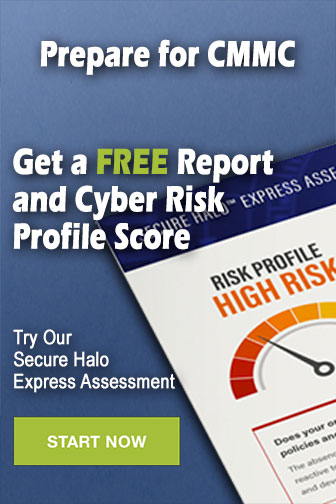