c.
Wipe out cavity of trap and accumulator bodies
with a lint free cloth dampened in solvent, per
Federal Specification P-D-680, Type II. Allow
bodies to air dry.
Take care not to damage the fine mesh
filter screen.
d.
Check the filter screen for damage such as
breaks and plugging due to corrosion; replace
filter assembly, if damaged.
e.
Check o-ring for deterioration, cuts, or other
damage. Replace as necessary.
f.
Install the o-ring and clean filter into top of trap
body. Do not overtighten.
5-13. Line Strainers (Figure 5-9). Each time the trap
filters are cleaned and inspected, refer to FIRST,
SECOND, AND THIRD STAGE TRAPS (Section V).
The line strainers shall be cleaned and inspected. To
clean and inspect the line strainers, proceed as follows:
NOTE
For best results, use Ultrasonic Cleaner, NSN 4940-00-
164-8977, (Table 2-1), to clean strainers and filters.
a.
From first and second stage line strainers,
unscrew and remove the body plug, o-ring,
washer, and filter element. From third stage,
unscrew and remove the plug and screen
assembly and o-ring.
Provide adequate ventilation when using
dry
cleaning
solvent
(Federal
Specification P-D- 680, Type II). Avoid
prolonged
breathing
of
vapors
and
minimize skin contact.
b.
Wash line strainer filter elements and screen
filter in- solvent, per Federal Specification P-D-
680, Type II. Allow filter clement to air dry.
c.
Inspect elements and filter for any damage.
Replace as necessary.
d.
Check all o-rings and seal washers for any
damage; replace as necessary.
e.
Install
o-ring
and
clean
plug
and
screen
assembly in third stage line strainer. Install
element, seal washer, and body plug in first and
second stage line filters.
f.
After compressor is started, check for leakage
around plugs with a soapy water solution applied
with a brush. Plug is leaking of solution bubbles.
5-14. Clutch Adjusting Yoke Adjustment (Figure 5-10).
When clutch adjustment is necessary, disengage clutch
by pulling the CLUTCH operating rod on the control
panel, away from control panel and proceed as follows:
a.
Remove the four screws and lockwashers
attaching the handhold cover to clutch housing
assembly. Remove cover.
b.
Using
START
switch,
rotate
the
engine
crankshaft
until
the
adjusting
lock
pin
is
accessible. Place a 1/16 inch thick washer of
sufficient diameter over the lock pin.
c.
Using
clutch
adjustment
tool
(Table
2-1)
disengage the lock pin from the floating plate.
Insert cotter pin. Or equivalent, in the cross-
drilled hole in the lock pin. Allow the cotter pin in
the lock pin to come to rest on the washer; the
lock pin is now locked in the out position.
d.
Using the clutch adjustment tool, turn the
adjusting yoke in a clockwise direction until the
lock pin in the adjusting yoke has passed one or
two adjusting holes in the floating plate.
e.
Remove the cotter pin and washer from lock pin
and allow lock pin to seat in adjusting hole in
floating plate.
f.
Engage clutch. A distinct pressure should be felt
when clutch is engaged. If not, repeat steps a
through e until pressure is felt.
g.
Replace
clutch
housing
cover
and
install
washers and screws removed in step a.
5-15. Clutch Operating Rod Adjustment (Figure 5-11).
Each time the clutch adjusting yoke is adjusted, refer to
CLUTCH ADJUSTING YOKE ADJUSTMENT (Section
V), the clutch operating rod shall be adjusted. To adjust
the clutch operating rod, proceed as follows:
a.
Remove cotter pin and clevis pin.
b.
Loosen jam nut on clutch operating rod, turn rod
yoke farther on to clutch operating rod or off on
rod to shorten or lengthen effective stroke of
clutch operating rod.
5-10
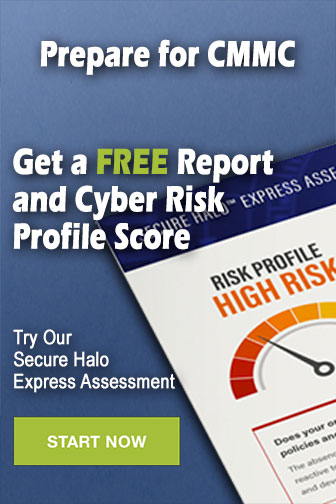