CHAPTER 1. GENERAL INFORMATION, EQUIPMENT DESCRIPTION AND THEORY OF OPERATION FOR SHEET METAL SHOPGENERAL INFORMATIONPREPARATION FOR STORAGE OR SHIPMENTLIST OF ABBREVIATIONS/ACRONYMSSAFETY, CARE, AND HANDLINGSUPPORTING INFORMATION FOR REPAIR PARTS, SPECIAL TOOLS, TMDE, AND SUPPORT EQUIPMENTFigure 1. Sheet Metal Shop.Figure 2. Expanded Wall Transport Mode Component View (SC4920-99-A68).Figure 3. Expanded Wall Transport Mode Component View (1035658).Figure 4. Fixed Wall Transport Mode Component View (SC4920-99-A68 and 1035658).Figure 5. Operational Mode Component View (SC4920-99-A68).Figure 6. Operational Mode Component View (1035658).DIFFERENCES BETWEEN MODELSTHEORY OF OPERATIONCHAPTER 2. OPERATOR INSTRUCTIONS FOR SHEET METAL SHOPDESCRIPTION AND USE OF OPERATOR CONTROLS AND INDICATORSTable 1. Oil/Water Separator Controls and Indicators.OPERATION UNDER USUAL CONDITIONS: SITING REQUIREMENTSFigure 1. Leveling Support Jack.Figure 2. Leveling Support Jack Install.Figure 3. Load Balancer Slide Stops, Upper Positions.Figure 4. Cam Lock Handles.Figure 5. Load Balancer Slide Stops, Lower Position.Figure 7. Sidewall Support Brace.Figure 8. Hinged Jack Assemblies.Figure 9. Hinged Jack Assemblies Extensions.Figure 10. Positioning Hinged Jack Extensions.Figure 11. Solar Bar Handles.Figure 12. Raising Hinged Roof.Figure 13. Positioning Roof and Hinged End Walls.Figure 14. Hinged Roof Support Strut Assemblies.Figure 15. Shelter Leveling.Figure 16. Remove Sidewall Support Braces.CONNECTING POWER TO THE SHELTERFigure 2. Connecting PDB to Generator.Figure 3. Main Circuit Breaker.Figure 4. Relocation of Cable Reel Assembly and 100 amp Power Cable Assembly.Figure 5. Extending Main Power Cable.Figure 7. Connecting Main Power Cable to PDB.INSTALL LIGHTINGFigure 2. Installing Ceiling Lights.Figure 3. Connecting Ceiling Lights.Figure 4. Installing Cable and Receptacle Assembly.Figure 5. Installing Area Light.PREPARING SHELTER FOR ECU INSTALLATIONFigure 1. Hinged Floor Cable Guide Housing Removal.Figure 2. Hinged Floor Cable Guide Housing Reinstall.Figure 3. Removing Plugs on ECU Fold-down Panel.Figure 4. ECU Fold-down Panel Latches.Figure 6. Installing T-Seal.OPENING ECU FOLD-DOWN PANELS - CONTINUEDSAFEGUARDING ATTACHING HARDWAREPOSITIONING SHELTER BASIC ISSUE ITEMS (BII) BOX FOR OPERATIONAL MODEPOSITIONING ECU S FOR OPERATIONAL MODEFigure 1. Unsecure ECU (A).Figure 2. Placing ECU (A) on ECU Fold-down Panel.Figure 4. Aligning Bolt Holes of ECU (A) with ECU Fold-down Panel.POSITIONING ECU (B) FOR OPERATIONAL MODEFigure 6. Unsecure ECU (B).Figure 7. Placing ECU (B) on ECU Fold-down Panel.Figure 9. Aligning Bolt Holes of ECU (B) with ECU Fold-down Panel.Figure 11. Connecting Power to ECU s.POSITIONING EYEWASH STATION FOR OPERATIONAL MODEFigure 1. Unsecure Eyewash Station.Figure 2. Position Eyewash Station.POSITIONING THROATLESS SHEARING MACHINE FOR OPERATIONAL MODEFigure 1. Unsecure Throatless Shearing Machine.POSITIONING THROATLESS SHEARING MACHINE FOR OPERATIONAL MODE - CONTINUEDPOSITIONING FOUR DRAWER CABINET (A) (SC4920-99-A68) OR SIX DRAWER CABINET (A) (1035658) - FOR OPERATIONAL MODEFigure 1. Unsecure Cabinet (A).POSITIONING FOUR DRAWER CABINET (A) (SC4920-99-A68) OR SIX DRAWER CABINET (A) (1035658) - FOR OPERATIONAL MODE - ContinuedPOSITIONING STRAIGHT STOOLS FOR OPERATIONAL MODEFigure 1. Unsecure Straight Stools.POSITIONING STRAIGHT STOOLS FOR OPERATIONAL MODE - CONTINUEDPOSITIONING SHELF CABINET (B) FOR OPERATIONAL MODEPOSITIONING SHELF CABINET (B) FOR OPERATIONAL MODE - ContinuedPOSITIONING SHELF CABINET (C) FOR OPERATIONAL MODEPOSITIONING SHELF CABINET (C) FOR OPERATIONAL MODE - ContinuedPOSITIONING BAND SAW FOR OPERATIONAL MODEFigure 1. Unsecure Band Saw.POSITIONING BAND SAW FOR OPERATIONAL MODE - CONTINUEDPOSITIONING STAKE SUPPORT TABLE FOR OPERATIONAL MODEFigure 1. Unsecure Stake Support Table.POSITIONING STAKE SUPPORT TABLE FOR OPERATIONAL MODE - CONTINUEDCONNECTING COMPRESSED AIR AND WATERFigure 2. Connecting Compressed Air.CHECKING SHELTER LEVELDISCONNECTING COMPRESSED AIR AND WATERFigure 2. Replacing Protective Dust Cap.DISCONNECTING COMPRESSED AIR - CONTINUEDPOSITIONING ECUS FOR TRANSPORT MODEFigure 2. Removing ECU (B) Hardware from ECU Fold-down Panel.Figure 3. Secure ECU (B).Figure 4. Removing ECU (A) Hardware from ECU Fold-down Panel.Figure 5. Secure ECU (A).POSITIONING SHELTER BII BOX FOR TRANSPORT MODEPOSITIONING EYEWASH STATION ASSEMBLY BRACKET AND HARDWARE FOR TRANSPORT MODEFigure 1. Secure Eyewash Station Assembly Bracket and Hardware.POSITIONING EYEWASH STATION ASSEMBLY BRACKET AND HARDWARE FOR TRANSPORT MODE - ContinuedPOSITIONING STAKE SUPPORT TABLE FOR TRANSPORT MODEFigure 1. Secure Stake Support Table.POSITIONING STAKE SUPPORT TABLE FOR TRANSPORT MODE - CONTINUEDPOSITIONING BAND SAW FOR TRANSPORT MODEFigure 1. Secure Band Saw.POSITIONING BAND SAW FOR TRANSPORT MODE - CONTINUEDPOSITIONING SHELF CABINET (C) FOR TRANSPORT MODEPOSITIONING SHELF CABINET (C) FOR TRANSPORT MODEPOSITIONING SHELF CABINET (C) FOR TRANSPORT MODE - CONTINUEDPOSITIONING SHELF CABINET (B) FOR TRANSPORT MODEPOSITIONING SHELF CABINET (B) FOR TRANSPORT MODE - CONTINUEDPOSITIONING FOUR DRAWER CABINET (A) (SC4920-99-A68) OR SIX DRAWER CABINET (A) (1035658) FOR TRANSPORT MODEPOSITIONING FOUR DRAWER CABINET (A) (SC4920-99-A68) OR SIX DRAWER CABINET (A) (1035658) FOR TRANSPORT MODE - ContinuedPOSITIONING FOUR DRAWER CABINET (A) (SC4920-99-A68) OR SIX DRAWER CABINET (A) (1035658) FOR TRANSPORT MODE - ContinuedPOSITIONING STRAIGHT STOOLS FOR TRANSPORT MODEFigure 1. Secure Straight Stools.POSITIONING THROATLESS SHEARING MACHINE FOR TRANSPORT MODEFigure 1. Secure Throatless Shearing Machine.POSITIONING THROATLESS SHEARING MACHINE FOR TRANSPORT MODE - CONTINUEDPREPARING SHELTER FOR ECU STOWAGEFigure 2. Closing ECU Fold-down Panel.Figure 4. Installing Plugs on ECU Fold-down Panel.Figure 6. Hinged Floor Cable Guide Housing Installation.DISCONNECTING POWER FROM SHELTERFigure 2. Disconnecting Main Power Cable from PDB.Figure 3. Disconnecting Main Power Cable from Shelter.Figure 4. Securing Cable Reel Assembly.Figure 5. Disconnecting PDB from Generator.Figure 6. Removing External Grounding Rod.REMOVING LIGHTINGFigure 2. Removing Cable and Receptacle Assembly.Figure 3. Repositioning Ceiling Lights.PREPARING SHELTER FOR TRANSPORTFigure 2. Removing Sidewall Support Braces.Figure 3. Lowering Shelter Roof.Figure 4. Secure Support Strut Assemblies.Figure 6. Hinged Jack Assemblies Extension.Figure 7. Load Balancers Slide Stops, Upper Position.Figure 8. Cam Lock Handles.Figure 9. Load Balancers Slide Stops, Lower Position.Figure 10. Lowering Leveling Support Jack Assemblies.Figure 11. Stowing Leveling Support Jack Assemblies.OPERATION UNDER UNUSUAL CONDITIONSFigure 2. Installing Ground Anchors.Figure 3. Loops and Clamps Installation.Figure 4. Securing Loops and Clamps.OPERATION IN SNOW, ICE OR EXTREME COLDOPERATION FOR IMPROVING SOIL CONDUCTIVITY FOR SHELTER GROUNDINGCHAPTER 3. FIELD LEVEL MAINTENANCE TROUBLESHOOTING PROCEDURES FOR SHEET METAL SHOPTROUBLESHOOTING PROCEDURESCHAPTER 4. FIELD LEVEL MAINTENANCE INSTRUCTIONS FOR SHEET METAL SHOPSERVICE UPON RECEIPTPREVENTIVE MAINTENANCE CHECKS AND SERVICE (PMCS) INTRODUCTIONCorrosion Prevention and Control (CPC)PREVENTIVE MAINTENANCE CHECKS AND SERVICE (PMCS)Table 1. Field Level Preventive Maintenance Checks and Services for Sheet Metal ShopTable 1. Field Level Preventive Maintenance Checks and Services for Sheet Metal Shop. - ContinuedTable 1. Field Level Preventive Maintenance Checks and Services for Sheet Metal Shop. - ContinuedTable 1. Field Level Preventive Maintenance Checks and Services for Sheet Metal Shop. - ContinuedTable 1. Field Level Preventive Maintenance Checks and Services for Sheet Metal Shop. - ContinuedTable 1. Field Level Preventive Maintenance Checks and Services for Sheet Metal Shop. - ContinuedMAINTENANCE INSTRUCTIONS FOR CABINET ASSEMBLIESFigure 2. Drawers, Slides, and Shelves Remove and Install.DRAWERS, SLIDES, AND SHELVESFOUR DRAWER CABINET (A) (SC4920-99-A68) OR SIX DRAWER CABINET (A) (1035658)FOUR DRAWER CABINET (A) (SC4920-99-A68) OR SIX DRAWER CABINET (A) (1035658)INSPECTION OF INSTALLED ITEMSINSPECTION OF INSTALLED ITEMS CONTINUEDSHELF CABINET (B) CONTINUEDINSPECTION OF INSTALLED ITEMSREPAIR OR REPLACEMENTINSTALLATION CONTINUEDFOUR DRAWER CABINET (D), SIX DRAWER CABINET (E), AND FOUR DRAWER CABINET (F)FOUR DRAWER CABINET (D), SIX DRAWER CABINET (E), AND FOUR DRAWER CABINET (F) CONTINUEDFOUR DRAWER CABINET (D), SIX DRAWER CABINET (E), AND FOUR DRAWER CABINET (F)FOUR DRAWER CABINET (D), SIX DRAWER CABINET (E), AND FOUR DRAWER CABINET (F) - ContinuedMAINTENANCE INSTRUCTIONS FOR CABINET INTEGRATION HARDWAREMAINTENANCE INSTRUCTIONS FOR CABINET INTEGRATION HARDWARE - ContinuedMAINTENANCE INSTRUCTIONS FOR CABINET INTEGRATION HARDWARE - ContinuedMAINTENANCE INSTRUCTIONS FOR CABINET INTEGRATION HARDWARE - ContinuedMAINTENANCE INSTRUCTIONS FOR CABINET INTEGRATION HARDWARE - ContinuedMAINTENANCE INSTRUCTIONS FOR UPRIGHT DRILLING MACHINE AND HARDWAREMAINTENANCE INSTRUCTIONS FOR UPRIGHT DRILLING MACHINE AND HARDWARE - ContinuedMAINTENANCE INSTRUCTIONS FOR BENCH GRINDER AND HARDWAREMAINTENANCE INSTRUCTIONS FOR BENCH GRINDER AND HARDWARE - ContinuedMAINTENANCE INSTRUCTIONS FOR MACHINIST VISE AND HARDWAREMAINTENANCE INSTRUCTIONS FOR THROATLESS SHEARING MACHINE, ANVIL/THROATLESS SHEAR STAND ASSEMBLY AND HARDWAREFigure 1. Throatless Shearing Machine and Hardware.Figure 2. Anvil/Shear Stand Assembly and Hardware.ANVIL/THROATLESS SHEAR STAND ASSEMBLYMAINTENANCE INSTRUCTIONS FOR STAKEHOLDER BENCH PLATE AND STAKE SUPPORT TABLE AND HARDWAREMAINTENANCE INSTRUCTIONS FOR STAKEHOLDER BENCH PLATE AND STAKE SUPPORT TABLE AND HARDWARE - ContinuedFigure 2. Stake Support Table Assembly and Hardware.STAKE SUPPORT TABLE ASSEMBLY AND HARDWARE CONTINUEDMAINTENANCE INSTRUCTIONS FOR SHEET METAL FORMING MACHINE, TUBE, AND HARDWAREFigure 1. Sheet Metal Forming Machine and Hardware.REPAIR OR REPLACEMENTMAINTENANCE INSTRUCTIONS FOR BAND SAW BRACKETS AND HARDWAREFigure 1. Band Saw Brackets and Hardware.MAINTENANCE INSTRUCTIONS FOR BAND SAW BRACKETS AND HARDWARE - ContinuedMAINTENANCE INSTRUCTIONS FOR SHEET METAL BRAKE MACHINE TABLE AND HARDWAREFigure 1. Sheet Metal Brake Machine Table and Hardware.MAINTENANCE INSTRUCTIONS FOR SHEET METAL BRAKE MACHINE TABLE AND HARDWARE - ContinuedMAINTENANCE INSTRUCTIONS FOR SHRINKING/STRETCHING MACHINE BRACKETS AND HARDWAREMAINTENANCE INSTRUCTIONS FOR SHRINKING/STRETCHING MACHINE BRACKETS AND HARDWARE - ContinuedMAINTENANCE INSTRUCTIONS FOR SHEARING MACHINE BRACKETS AND HARDWAREFigure 1. Shearing Machine Brackets and Hardware.MAINTENANCE INSTRUCTIONS FOR SHEARING MACHINE BRACKETS AND HARDWARE - ContinuedFigure 2. Shearing Machine Support Bar and Back Support Brackets and Hardware.MAINTENANCE INSTRUCTIONS FOR SHEARING MACHINE BRACKETS AND HARDWARE - ContinuedMAINTENANCE INSTRUCTIONS FOR EYEWASH STATION ASSEMBLY BRACKET AND HARDWAREFigure 1. Eyewash Station.MAINTENANCE INSTRUCTIONS FOR SETSCREWS AND INSERTSFigure 2. Wall and Floor Insert Inspection.MAINTENANCE INSTRUCTIONS FOR BAYONET NEILL- CONCELMAN (BNC) CONNECTOR ASSEMBLYFigure 2. Replace BNC Connector Assembly.MAINTENANCE INSTRUCTIONS FOR BAYONET NEILL- CONCELMAN (BNC) CONNECTOR ASSEMBLYMAINTENANCE INSTRUCTIONS FOR FIRST AID BRACKET ASSEMBLY AND HARDWAREFigure 1. First Aid Bracket Assembly.MAINTENANCE INSTRUCTIONS FOR FIRST AID BRACKET ASSEMBLY AND HARDWARE - ContinuedMAINTENANCE INSTRUCTIONS FOR 60 AMP RECEPTACLEMAINTENANCE INSTRUCTIONS FOR 60 AMP RECEPTACLE - ContinuedFigure 2. Inspect 45 Degree Angle Adapter.Figure 4. 45 Degree Angle Adapter Replacement.Figure 5. 45 Degree Angle Adapter Removal from Power Entry Panel Cover.45 DEGREE ANGLE ADAPTER CONTINUEDMAINTENANCE INSTRUCTIONS FOR ECU POWER CABLE ASSEMBLYFigure 1. Testing ECU Power Cable.Figure 2. Removing ECU Power Cable.ECU POWER CABLE CONTINUEDFigure 3. Replacing ECU Power Cable.Figure 4. Box Connector.Figure 5. Box Connector Replacement.BOX CONNECTOR FOR ECU POWER CABLE CONTINUEDFigure 6. Electrical Plug Connector.ELECTRICAL PLUG CONNECTOR CONTINUEDMAINTENANCE INSTRUCTIONS FOR CIRCUIT BREAKERSFigure 1. Testing Circuit Breakers.Figure 2. Replacing Circuit Breakers.MAINTENANCE INSTRUCTIONS FOR CIRCUIT BREAKERS - ContinuedMAINTENANCE INSTRUCTIONS FOR DOOR LOCK TABSFigure 2. Door Lock Tabs Placement.Figure 3. Door Lock Tabs Installation.MAINTENANCE INSTRUCTIONS FOR WATER AND AIR FEED-THRU CONNECTOR ASSEMBLIESFigure 2. Disassembly of Water Feed-thru Connector Assembly.Figure 4. Water Feed-thru Connector Flange.Figure 6. Attach Water Feed-Thru Connector Assembly.Figure 7. Inspect Air Feed-thru Connector Assembly.Figure 9. Removal of Air Feed-thru Connector Assembly.Figure 11. Install Air Feed-thru Connector Assembly.MAINTENANCE INSTRUCTIONS FOR FIRE EXTINGUISHER BRACKETS AND HARDWAREMAINTENANCE INSTRUCTIONS FOR FIRE EXTINGUISHER BRACKETS AND HARDWARE - ContinuedMAINTENANCE INSTRUCTIONS FOR OIL/WATER SEPARATORFigure 2. Hose Clamp Removal.Figure 4. Hose Removal.Figure 6. Hose Reinstallation.Figure 8. Inspect Oil/Water Separator.MAINTENANCE INSTRUCTIONS FOR ECU CABLE ASSEMBLYMAINTENANCE INSTRUCTIONS FOR ECU SECURITY SCREENSMAINTENANCE INSTRUCTIONS FOR ECU SECURITY SCREENS - ContinuedMAINTENANCE INSTRUCTIONS FOR GROUND RODFigure 2. Test Ground Rod.MAINTENANCE INSTRUCTIONS FOR GROUND ROD - ContinuedILLUSTRATED LIST OF MANUFACTURED ITEMSFigure 1. Stake Support Table Assembly (Sheet 1 of 10).Figure 1. Stake Support Table Assembly (Sheet 2 of 10).Figure 1. Stake Support Table Assembly (Sheet 3 of 10).Figure 1. Stake Support Table Assembly (Sheet 4 of 10).Figure 1. Stake Support Table Assembly (Sheet 5 of 10).Figure 1. Stake Support Table Assembly (Sheet 6 of 10).Figure 1. Stake Support Table Assembly (Sheet 7 of 10).Figure 1. Stake Support Table Assembly (Sheet 8 of 10).Figure 1. Stake Support Table Assembly (Sheet 9 of 10).Figure 1. Stake Support Table Assembly (Sheet 10 of 10).Figure 2. Shearing Machine Bracket Assembly (Sheet 1 of 4).Figure 2. Shearing Machine Bracket Assembly (Sheet 2 of 4).Figure 2. Shearing Machine Bracket Assembly (Sheet 3 of 4).Figure 2. Shearing Machine Bracket Assembly (Sheet 4 of 4).Figure 3. Sheet Metal Brake Support Table Assembly (Sheet 1 of 9).Figure 3. Sheet Metal Brake Support Table Assembly (Sheet 2 of 9).Figure 3. Sheet Metal Brake Support Table Assembly (Sheet 3 of 9).Figure 3. Sheet Metal Brake Support Table Assembly (Sheet 4 of 9).Figure 3. Sheet Metal Brake Support Table Assembly (Sheet 5 of 9).Figure 3. Sheet Metal Brake Support Table Assembly (Sheet 6 of 9).Figure 3. Sheet Metal Brake Support Table Assembly (Sheet 7 of 9).Figure 3. Sheet Metal Brake Support Table Assembly (Sheet 8 of 9).Figure 3. Sheet Metal Brake Support Table Assembly (Sheet 9 of 9).Figure 4. Shrinking/Stretching Machine Bracket.Figure 5. Cabinet Bracket.Figure 6. Shearing Machine Bracket.Figure 7. Shear Support Bar Brackets (Sheet 1 of 2).Figure 7. Shear Support Bar Brackets (Sheet 2 of 2).Figure 8. Washer.Figure 9. Band Saw Bracket.Figure 10. First Aid Kit Bracket (Sheet 1 of 3).Figure 10. First Aid Kit Bracket (Sheet 2 of 3).Figure 10. First Aid Kit Bracket (Sheet 3 of 3).Figure 11. Anvil/Throatless Shear Stand Assembly (Sheet 1 of 4).Figure 11. Anvil/Throatless Shear Stand Assembly (Sheet 2 of 4).Figure 11. Anvil/Throatless Shear Stand Assembly (Sheet 3 of 4).Figure 11. Anvil/Throatless Shear Stand Assembly (Sheet 4 of 4).TORQUE LIMITSCHAPTER 5. SUPPORTING INFORMATION FOR SHEET METAL SHOPREFERENCESMAINTENANCE ALLOCATION CHART (MAC) INTRODUCTIONAviation Support Company (ASC) Maintenance FunctionsMaintenance Functions - ContinuedExplanations of Entries in the MACExplanation of Entries in the Tools and Test Equipment RequirementsMAINTENANCE ALLOCATION CHART (MAC)Table 1. MAC for Sheet Metal Shop ContinuedTable 1. MAC for Sheet Metal Shop ContinuedTable 1. MAC for Sheet Metal Shop ContinuedTable 2. Tools And Test Equipment Requirements For Sheet Metal Shop.REPAIR PARTS AND SPECIAL TOOLS LIST (RPSTL) INTRODUCTIONEXPLANATION OF COLUMNS IN THE REPAIR PARTS LIST AND SPECIAL TOOLS LIST WORK PACKAGESMaintenance CodeRecoverability CodeEXPLANATION OF CROSS-REFERENCE INDEXES WORK PACKAGES FORMAT AND COLUMNSSpecial InformationHOW TO LOCATE REPAIR PARTSREPAIR PARTS AND SPECIAL TOOLS LISTFigure 1. Sheet Metal Shop Set.Figure 2. Sheet Metal Shop Set Equipment Installation.Figure 2. Sheet Metal Shop Set Equipment Installation. - ContinuedFigure 2. Sheet Metal Shop Set Equipment Installation. - ContinuedFigure 3. Sheet Metal Cabinet Assembly.Figure 3. Sheet Metal Cabinet Assembly. - ContinuedFigure 4. Sheet Metal Cabinet Assembly.Figure 5. Sheet Metal Cabinet Assembly.Figure 5. Sheet Metal Cabinet Assembly. - ContinuedFigure 6. Sheet Metal Cabinet Assembly.Figure 6. Sheet Metal Cabinet Assembly. - ContinuedFigure 7. Sheet Metal Cabinet Assembly.Figure 7. Sheet Metal Cabinet Assembly. - ContinuedFigure 8. Sheet Metal Forming Machine.Figure 8. Sheet Metal Forming Machine. - ContinuedFigure 9. Band Saw.Figure 10. Sheet Metal Brake Machine.Figure 10. Sheet Metal Brake Machine. - ContinuedFigure 11. Shrinking Stretching Machine.Figure 11. Shrinking Stretching Machine. - ContinuedFigure 12. Shearing Machine.Figure 12. Shearing Machine. - ContinuedFigure 13. 100 amp Shelter (Sheet 1 of 2).Figure 13. 100 amp Shelter (Sheet 2 of 2).Figure 13. 100 amp Shelter - ContinuedFigure 13. 100 amp Shelter - ContinuedFigure 14. BNC Connector Assembly.Figure 15. Electrical Installation.Figure 15. Electrical Installation. - ContinuedFigure 16. Oil and Water Separator.Figure 16. Oil and Water Separator. - ContinuedFigure 17. ECU Cable Assembly.Figure 18. Ground Rod.NATIONAL STOCK NUMBER INDEXNATIONAL STOCK NUMBER INDEX - ContinuedPART NUMBER INDEXPART NUMBER INDEX - ContinuedPART NUMBER INDEX - ContinuedCOMPONENTS OF END ITEM (COEI) AND BASIC ISSUE ITEMS (BII) LISTSFigure 1. Components of End Item.Figure 2. BII Items (Sheet 1 of 2).Figure 2. BII Items (Sheet 2 of 2).Table 2. Basic Issue Items List.Table 2. Basic Issue Items List. Continued.Table 2. Basic Issue Items List. Continued.Table 2. Basic Issue Items List. Continued.Table 2. Basic Issue Items List. Continued.EXPENDABLE/DURABLE ITEMS LIST
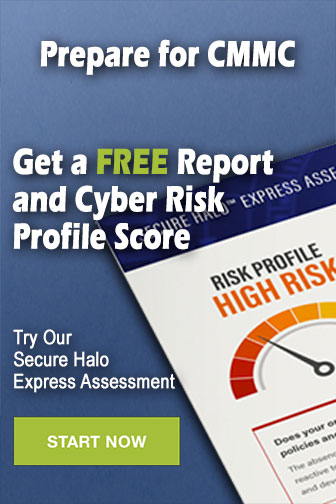